23.07.2019 10:14:00
The update of regulatory framework in the field of fire safety and the design of fire extinguishing systems affects both the objects under construction and the existing facilities. Already now reconstruction and technical re-equipment of oil and petroleum products warehouses (hereinafter referred to as oil depots) is taking place. These include tank farms, loading railcar racks, product pumping stations, consumable warehouses, storage warehouses for packaging products and other facilities that were equipped with fire extinguishing systems in the past decades according to the regulatory requirements of the 70-80s.
The subject of equipping industrial facilities with modern fire extinguishing systems is a relevant one because the rules for confirming product compliance with fire safety requirements have changed. As new standards enter into force, demand for effective fire protection systems will only increase.
The article discusses differences between the oil depot fire extinguishing technologies, which were used in Russia in the 70-80s and at present, since about the 2000s. Pozhneftehim, a Russian manufacturer of equipment and foam concentrates for foam and water fire extinguishing systems, comments the modern solutions for the integrated protection of oil storage areas and other production facilities.
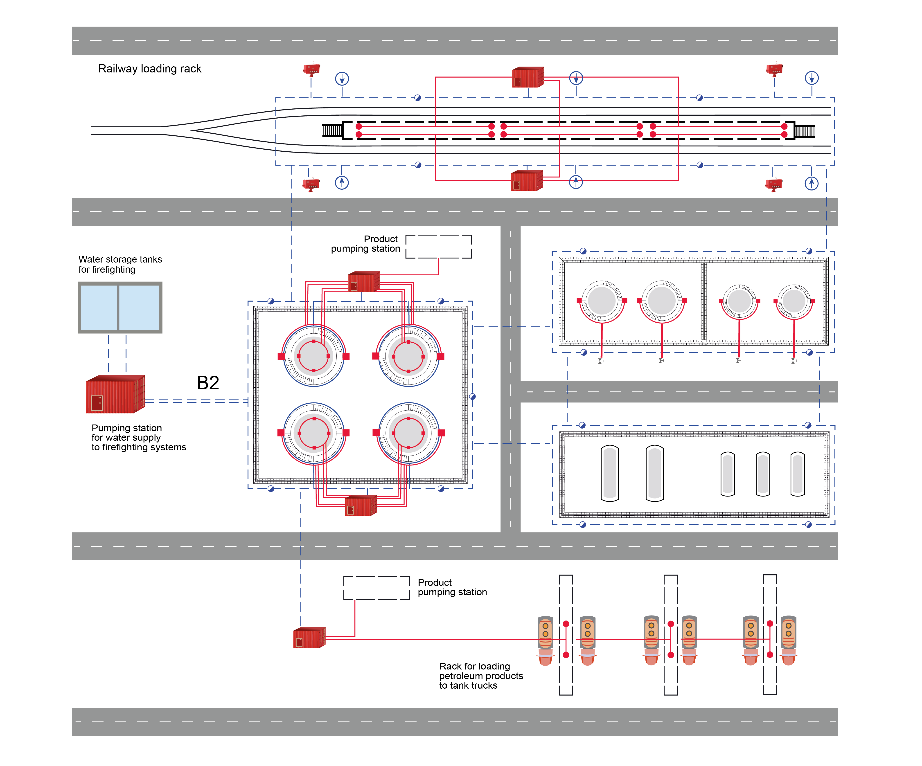
Problems with oil tank fire extinguishing systems
The common problems of fire protection and fire extinguishing systems of oil tanks, railcar loading racks, product pumping stations, buildings and premises as part of oil depots and oil refineries are as follows:
- deterioration of the outer ring foam and water pipelines;
- the use of filled main and distribution foam pipelines and the storage of a foam concentrate in solution (premix);
- low quality of the foam concentrate solution in networks, the need for its regular replacement and disposal;
- the use of obsolete and inefficient types of generators that are unstable to thermal effects;
- impossibility to conduct complex tests of stationary systems at existing production facilities.
The reconstruction of security systems at oil depots and oil refineries by recovering operability of active fire protection systems may cause difficulties. When expanding facilities, questions also concern the possible use of existing fire extinguishing systems’ capacity for new facilities.
We continue by considering modern effective fire extinguishing systems in comparison with the "classic" systems of the 70-90s at objects which form part of oil depots.
Tank farms
Tank farm firefighting: modern integrated fire protection systems
According to SP 5.13130.2009 (Table A.2) and SP 155.13130.2014 (paragraph 13.2.3), the oil tanks for ground storage of flammable and combustible liquids with a volume of 5000 m3 or more must be equipped with automatic foam fire extinguishing systems. The latter consist of a foam station with a foam concentrate storage and dosing system (SKhDP or bladder tank) and low expansion foam generators, such as Vega KNP, which supply the fire extinguishing substance to the fire source.
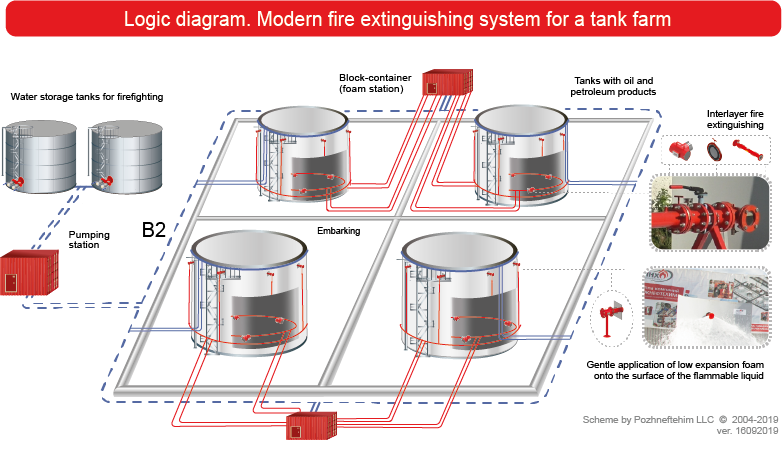
The advantage of modern fire extinguishing systems is the fluorosynthetic film-forming foam concentrate of AFFF, AFFF/AR, AFFF/AR LV types. Pozhneftehim produces this type of foam concentrates under the Aquafom brand, strictly according to the GOST R 53280 requirements. The use of fluorosynthetic film-forming foam concentrates is common in world practice.
AFFF, AFFF/AR, AFFF/AR LV foam concentrates form an insulating film (foam blanket) on the surface of the oil product, which gives burnback resistance and protects against explosions. Therefore, they are used for effective fire extinguishing of especially dangerous industrial facilities with storage and handling of flammable and combustible liquids. In addition, the effectiveness of the AFFF, AFFF/AR, AFFF/AR LV foam concentrates is demonstrated during the annual Advanced Courses of Pozhneftehim.
Modern foam generators, such as Vega low foam expansion chamber (KNP) or Shturm high-pressure generator (VPG), are used to supply low expansion film-forming foam into the tank. Vega KNP feeds foam onto the surface of the oil product and Shturm VPG feeds foam into the oil layer.
The Vega low expansion foam chamber is designed to extinguish fires in tanks with highly flammable and combustible liquids. With minimum overall dimensions, the width of the foam fan when installed at a height of 2.5 m is at least 12 m, and at a height of 6 m it is at least 15 m. The low expansion chamber includes a sealing element that eliminates the presence of oil vapor inside the foam chamber. The design of the generator also provides for the possibility of testing without removing the KNP from the tank.
Interlayer fire suppression is recommended for tanks with a volume of 5000 m3 or more. The decision to choose the technology of foam supply into the fuel layer should be taken considering the type and viscosity of the oil product. The reason why this fire extinguishing method is recommended for use is the likely destruction of the upper belt of the tank in case of explosions (tank fires sometimes start with explosions). As a result of an explosion, the entire system for fire extinguishing on the surface of the oil product may be destroyed. Another reason is the likely partial collapse of the tank lid, as a result of which the foam that will be supplied from above will not reach the source of ignition.
The Shturm high-pressure foam generator, the Interlayer nozzle and the burstable membrane are used in modern system of interlayer fire suppression. The suitable fire extinguishing agent is the film-forming low expansion foam, which is obtained from AFFF foam concentrates. The standard intensity for the supply of foam solution into the layer is indicated in SP 155.13130.2014.
In addition, according to paragraph 13.2.8 of SP 155.13130.2014, the tanks are equipped with stationary cooling units with manual start. In the upper zone of the tanks, irrigation rings are installed. The Fire monitor complex (LPK), consisting of a fire tower, a fire monitor and a water-film screen can be used for water cooling of tanks (burning and adjacent to burning) in some systems.
Tank farm fire extinguishing: the “classic” system as in the 70-80s
The main difference between the classic and the modern systems is the extinguishing method. Previously, the fire suppression systems for flammable and combustible liquids usually required the medium expansion foam. This can extinguish fuels provided that the type of foam concentrate is selected correctly and the entire fire extinguishing system is operable. However, it does not give burnback resistance, nor protects against explosions.
The previously widespread GPS and GPSS medium foam generators are still present at hazardous industrial facilities. They have an attractive price. Nevertheless, practice shows that they do not withstand the effects of an open flame (the grid quickly collapses from fire). In addition, tests demonstrate that the GPSS generator does not convert part of the premix into the foam. Therefore, flow errors occurs, which may lead to ineffective foam attacks.
At present, medium expansion foam continues to be used. However, to guarantee the effectiveness of a foam attack, you need the foam concentrate produced strictly according to GOST, the system must not have filled foam pipelines and the foam generators must be resistant to open flame at least during the response time of the system (the supply of extinguishing agent must begin in within 3 minutes).
The use of medium expansion foam has introduced restrictions for extinguishing oil with impurities of gas condensate and for oil products derived from gas condensate, as well as for extinguishing gasoline containing polar liquids, marine fuel, jet fuel, etc. in accordance with the requirements of tab. 1 SP 155.13130.2014.
Railcar loading racks for fuel transfer
Fire extinguishing of fuel transfer railcar racks: a modern integrated fire protection system
SP 155.13130.2014 governing the loading and unloading railcar racks specifies the use of stationary (non-automatic) foam fire extinguishing installations. The latter include a pumping station, a foam proportioning system with a foam concentrate storage and dosing system, a system of distributed foam pipelines (not filled with a foam concentrate solution), and low expansion foam generators.

Reliable thermo- and explosion-proof special deluge sprinklers should be used as foam generators. Pozhneftehim manufactures the Antifire special deluge sprinklers (universal water-foam spray nozzles) designed specifically for supplying low expansion foam to the source of ignition at highly dangerous explosive objects. The deluge sprinklers withstand temperatures from minus 60 to plus 800 °C, are resistant to aggressive environments and can be equipped with oscillators to increase the irrigation area.
The film-forming low expansion foam has increased efficiency compared to foam of medium expansion. Fluorosynthetic foam concentrates of AFFF, AFFF/AR or AFFF/AR LV types can be used in almost any foam fire extinguishing system. Pozhneftehim recommends the Aquafom IN or IIN foam concentrate for low expansion film-forming foam.
Stationary fire monitors are envisaged for fire protection of fuel transfer railway terminal (SP 155.13130.2014, clause 13.2.8). Pozhneftehim offers a integrated solution for remote cooling, the Antifire fire monitor complex (LPK) with a water screen. The application of LPK is regulated in accordance with paragraph 13.2.15 of SP 155.13130.2014.
Foam supply units are installed along the flyover every 120 meters (paragraph 5.1 of the VUP SNE). The Pozhneftehim equipment line has an effective solution, the Rubezh fire hose cabinet (BPG) for extracting water from ground fire pipelines and producing the foam solution for external firefighting. The Rubezh BPG for cold climate territories may have electric heating for pipelines, foam concentrate tanks, as well as a compartment for fire hoses.
Fire extinguishing of railcar loading racks: the “classic” system as in the 70-80s
At the end of the 20th century, fire extinguishing systems for fuel transfer railway terminals were equipped with GPS or GPSS generators. The medium expansion foam generators of this type are not heat-resistant and not explosion-proof. In addition, they are not equipped with oscillators. Therefore, when extinguishing tanks with flammable and combustible liquids, it is not guaranteed that the extinguishing agent enters directly into the neck of the tank.
Medium expansion foam obtained from the synthetic concentrates of S type is not suitable for extinguishing polar and mixed liquids. This is demonstrated at the Advanced training courses of Pozhneftehim, as we annually conduct fire tests with the extinguishing of flammable liquids by different types of foam concentrates. For effective fire suppression of highly flammable and combustible liquids of any type, modern film-forming foam concentrates of the AFFF/AR type and special Antifire deluge sprinklers are used.
The preferred substance for extinguishing highly flammable and combustible liquids at railcar racks is the low expansion foam. Current standards limit the use of medium expansion foam for extinguishing oil with impurities of gas condensate and for petroleum products derived from gas condensate, as well as for extinguishing gasoline containing polar liquids, marine fuel, jet fuel, etc. in accordance with the requirements of tab. 1 SP 155.13130.2014.
In addition, fire extinguishing systems for fuel transfer railway terminals as in 70-90s have the disadvantages of combining the pumping and foam stations in one room and filling foam pipelines with foam concentrate solution. All modern biodegradable foam concentrates lose their fire extinguishing ability in solution after 1-3 months. In case of fire, a liquid will be supplied for a long time, which does not have the fire extinguishing ability and complicates the extinguishing of the fire. The remoteness of the foam proportioners also does not contribute to the rapid supply of foam to the source of ignition. In modern fire extinguishing systems the foam stations are located close to protected objects, and the foam pipes are not filled with premix.
Firefighting of product pumping stations and warehouses: a modern system of integrated fire protection
Buildings, structures, premises, warehouses with oil and petroleum products are equipped with automatic fire extinguishing units (AUPT) in accordance with SP 5.13130.2009. In addition, SP 155.13130.2014 requires the installation of automatic fire extinguishing units at the following warehouse buildings (see Table 12):
Warehouse buildings |
Premises to be equipped with automatic fire extinguishing units |
Buildings of product pumping stations (except for tank farms of main oil pipelines), sewage pumping stations for pumping untreated industrial waste water (with oil and oil products) and trapped oil and oil products |
Premises for pumps and gate valve assemblies with a floor area of 300 m2 or more |
Buildings of pumping stations of tank farms of oil trunk pipelines |
Premises for pumps and gate valve assemblies at stations with a capacity of 1200 m3/h and more |
Warehouse buildings for the storage of petroleum products in containers |
Warehouses with an area of 500 m2 or more for petroleum products with a flash point of 120 °C and below, an area of 750 m2 or more - for other petroleum products |
Other warehouse buildings (filling, packaging, etc.) |
Industrial premises with an area of more than 500 m2, in which there are oil and oil products in an amount of more than 15 kg/m2 |
It is recommended to install modern fire extinguishing systems with low, medium or high expansion foam in warehouses, warehouse buildings and premises with storage and circulation of highly flammable and combustible liquids. Both synthetic and fluorosynthetic foam concentrates are acceptable. The choice of foam concentrates and equipment depends on the fire extinguishing technology and fire hazard of the facility (combustible material, water supply and other characteristics of the facility).
The logic diagram shows the components of the firefighting in general. Additional information on firefighting systems at warehouses is available on the Pozhneftehim website.
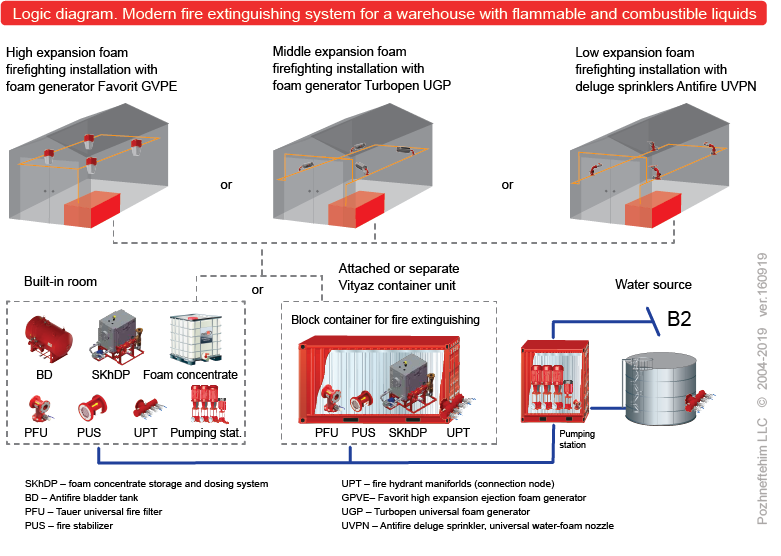
The introduction of a modern integrated fire protection system for a warehouse, a product pumping station and other premises as part of tank farms involves the development of a concept with the rationale for a suitable firefighting method. You can contact the specialists of Pozhneftehim for the development of the Fire Protection Concept.
Reconstruction of oil tank fire extinguishing system
Reconstruction of the fire extinguishing system starts with the development and approval of design documentation. If necessary, Pozhneftehim specialists develop Special technical conditions (STU) to determine compensatory measures and bring oil depot facilities in line with modern regulatory requirements. Special technical conditions may be required both for the construction of new oil depots, and for the reconstruction of existing ones which were build according to outdated requirements.
Pozhneftehim, a Russian manufacturer of equipment and foam concentrates, consults specialists on the design of fire extinguishing systems in accordance with the requirements of design documentation. The company's specialists also participate in commissioning tests of the fire extinguishing system at the customer’s facilities. You can find out more about the selection of modern effective foam and water fire extinguishing systems for tank farms, fuel transfer railway terminals, product pumping stations and warehouses from our specialists by phone (499) 703-01-32 or email mail@pnx-spb.ru.
Other news
The automated on-spot loading station (AUTN) is an automated technological facility for filling rail car tanks with liquid hydrocarbons in on-spot mode with movement of tanks for filling by a special shunting device which is an integral part of installation.
Production of equipment for firefighting systems
The customized production of firefighting equipment, the packaged supply of fire fighting installations (equipment + foam concentrate), supervised installation, start-up and commissioning of firefighting systems and installations.
Foam fire extinguishing. Pozhneftehim foam fire extinguishing installations
Foam fire extinguishing is a set of actions to eliminate fire. A foam or a wetting solutions are used as a fire extinguishing agent in foam fire extinguishing systems and installations.
Tank farm facility: firefighting systems
The update of regulatory framework in the field of fire safety and the design of fire extinguishing systems affects both the objects under construction and the existing facilities.
Pozhneftehim offers comprehensive solutions for fire protection of oil depots. The company designs fire extinguishing systems and develops Special technical conditions (STU) for hazardous industrial facilities: warehouses for highly flammable and combustible liquids, tank farms, railcar and truck loading / unloading racks.
Pozhneftehim. Production of high expansion foam generators
Pozhneftehim has been producing Favorit high expansion foam generators since 2010. The company provides comprehensive supplies of fire extinguishing units with high expansion foam generators (equipment + foam concentrate), as well as installation supervision, commissioning and maintenance at the customer’s site.
Water spray systems for fire protection of storage tanks, process vessels. Fixed water spray systems
Water spray is subject to the requirements of GOST R 12.3.047-98 Occupational Safety Standards System. Fire Safety of Technological Processes.
Water fire extinguishing. Pozhneftehim Water fire extinguishing installations
Water fire fighting is the most common way to extinguish fires.
Comments
Add first comment
Add comment
Add comment