FIREFIGHTING FOR LHG TANK FARMS. WATER COOLING OF LHG RESERVOIRS. FIRE PROTECTION SYSTEMS OF LIQUID HYDROCARBON GAS TANKS (STORAGES). FIRE RISK OF LHG STORAGE AND PROCESSING FACILITIES
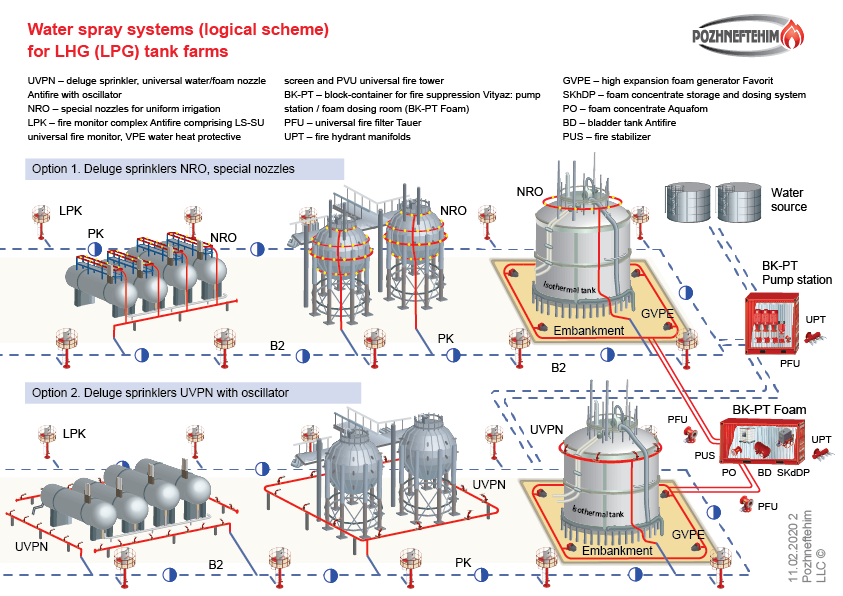
Pozhneftehim supports designing fire protection systems, manufactures equipment and foam concentrates for water cooling systems and installations, foam fire extinguishing of LHG storage and processing facilities.
More than 10 year experience of relations with leading oil and gas and petrochemical organizations provides an opportunity to to create highly effective fire protection systems.
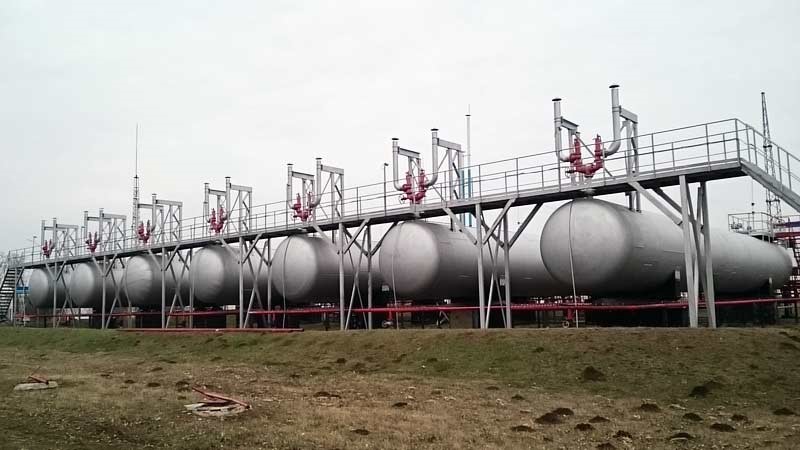
LHG tanks. Photo: газэкосеть.рф
Choose water spray system or water curtain
Facilities for storage and processing of liquefied hydrocarbon gases (LHG). General information
Facilities for LHG storage and processing include the following main objects of protection:
- compressor stations and pump rooms (см. see the section on fire extinguishing of compressor stations);
- компрессорные станции и насосные отделения (see the section on fire extinguishing of compressor stations);
- rail loading racks;
- finished products storages (LHG tank farms).
The LHG storage tanks under pressure in the standard version are suitable for propane, butane and propane-butane mixtures at wall temperatures from -40°C to +45°C.
Common are steel horizontal tanks with a volume of up to 200 m3, which are used for:
- LHG storage at gas filling stations and points (GNS and GNP);
- LHG storage at automobile gas and multi-fuel gas stations (AGZS and MTAZS);
- backup autonomous gas supply system for industrial and agricultural facilities;
- autonomous gasification of houses, cottages and cottage villages;
- as part of a farm of liquefied gas storage installations.
Spherical tanks and gasholders have capacities from 400 to 6,600 m3 and are intended for storage under pressure of various gaseous products, liquefied hydrocarbon gases (LHG), liquid products of chemical, gas and oil refining industries (butane-butylene, isopentane, hexane, ammonia, etc.) as well as inert gases and air.
Spherical tanks. Photo: Uralhimmash, uralhimmash.ru
There are a number of regulatory documents governing the requirements for LHG storage and processing. However, they relate mainly to small facilities with a total LHG storage volume of up to 8000 m3 and a single-unit tank capacity of up to 600 m3. At the same time, large-scale isothermal LHG storage facilities are operating with a single-unit tank capacity of up to 50,000 m3 and a total storage volume of up to 90,000 m3.
LHG tank farm (LHG storage) fire risk
In accordance with the recommendations “Ensuring fire safety of LHG storage and processing facilities”, VNIIPO of the Ministry of Internal Affairs of Russia, GUGPS of the Ministry of Internal Affairs of Russia and the EMERCOM Center for Strategic Studies of Civil Protection:
- when equipment is depressurized and LPG is released into the atmosphere due to the high evaporation rate, large air-vapor clouds can form, depending on the amount of instantly released gas or outflow velocity, as well as climatic conditions (wind speed, air temperature);
- since the vapor density of most LPGs is higher than the air density, vapor-air clouds can drift in the atmosphere surface layer over significant distances. When such clouds are ignited, they can quickly burn without explosion in the form of a flash or burn with an explosion with the compression wave formation;
- during depressurization of equipment where the liquefied gas is under pressure, steam-air jets are formed, and their ignition leads to the formation of fan-like jet flares, as well as jet torches close to axisymmetric. The impact of such torches, which are often of a great length, on the equipment leads to its damage and the involvement of more and more gas in the combustion process;
- the thermal effect of a jet fire or a burning spill on tanks with liquefied gas can lead to their destruction with the formation of fire balls with large radii of fatal damage to people by thermal radiation;
- when liquefied gases are stored in isothermal land-based storages, their possible destruction is of great danger. The resulting hydrodynamic wave can destroy the dike or overlap it with the formation of spills of large areas. During evaporation of liquefied gas from such a spill, large vapor-air clouds form. The burning of such spills can lead to fires at nearby facilities;
- One of the features of fires at the storage and processing facilities of liquefied petroleum gases is the development of possible chain of fire on the domino principle;
These basic provisions must be taken into account when developing fire protection systems.
Key equipment for active fire protection of LHG facilities
The main equipment providing active fire protection includes:
- automatic water spray installations;
- fire monitors;
- water curtains to limit spreading LHG vapor;
- foam extinguishing installations within the diking of isothermal tanks;
- water spray installations for rail LHG racks;
- high-expansion foam fire extinguishing systems in industrial buildings and premises.
Regulatory requirements and recommendations for fire fighting, water spraying of LHG tanks, LHG rail racks
GOST R 12.3.047-2012 Occupational safety standards system (SSBT). Fire safety of technological processes. General requirements. Control methods (requirements retrieval)
In raw materials, commodity and intermediate storages (parks), fire monitors are used to protect spherical and horizontal (cylindrical) tanks with liquefied hydrocarbon gases (LHG).
LHG tanks located in raw materials, commodity and intermediate storages (parks) in addition to fire monitors should have available automatic fixed water spray systems. The type, quantity and particulars of the arrangement of sprinklers of fixed water spray installations, as well as their operation mode (upstream pressure, water flow rate, water crown dispersion ability) should be selected based on the condition of uniform spray of all protected surfaces with a given intensity, providing thermal protection of equipment.
VUP SNE-87 (Industry-specific guidelines for designing railway loading racks) Departmental guidelines for designing rail loading racks for flammable and combustible liquids and liquefied hydrocarbon gases (requirements retrieval)
Water firefighting monitors should be provided for fire protection of railway loading racks handling liquefied hydrocarbon gases.
Comment:
A water cooling installation based on fire monitors is not effective under wind loads, as well as from the point of view of the need to spray areas closed to direct water jets. To eliminate these negative factors that can lead to the destruction and explosion of tanks with the formation of fire balls, Pozhneftehim, in addition to fire monitors, offers using sectional water spray systems based on the use of the Antifire special purpose deluge sprinklers (water/foam nozzles). These installations do not require the involvement in hazardous areas of personnel or employees of fire and rescue units. The Antifire fire monitors and sprinklers can be equipped with oscillating devices.
Recommendations "Ensuring fire safety of LHG storage and processing facilities" of VNIIPO of the Ministry of Internal Affairs of Russia, GUGPS of the Ministry of Internal Affairs of Russia and the EMERCOM Center for Strategic Studies of Civil Protection of Russia (requirements retrieval)
Fire protection systems of an LHG isothermal tank
Isothermal tank. Photo: Cascade Metal, www.emkostnoe.ru
Water spray of LHG isothermal tank
To prevent escalation of an accident accompanied by a fire, isothermal LHG storage tanks should be equipped with automatic water spray installations that provide protection for:
- tank roof and side surfaces;
- tank mounted fittings, pipelines, valves and equipment;
- equipment and structures of reservoir working sites;
- check, shut-off and operational valves on the pipelines for supply and takeoff of LHG and gas, as well as overhead pipelines and metal supporting structures;
- pumps and equipment for LHG pumpout.
The type, quantity and particulars of the sprinklers arrangement, as well as their operation mode (pressure upstream the sprinklers, water rate) should be determined by the design documents based on the condition of uniform spraying of all protected surfaces and reliable thermal protection of tank and equipment structures as in the case of LHG spill and combustion within own buffer zone, and during radiation thermal effects of LHG burning leaks.
In addition to fixed automatic water spraing systems, it should be possible to spray the roof surface and the tank mounted equipment from fire monitors, provided that each point of the tank is sprayed with one jet.
Fire monitors for spraying aboveground tanks should be automated or remotely controlled.
Localization of LHG vapor, water curtains
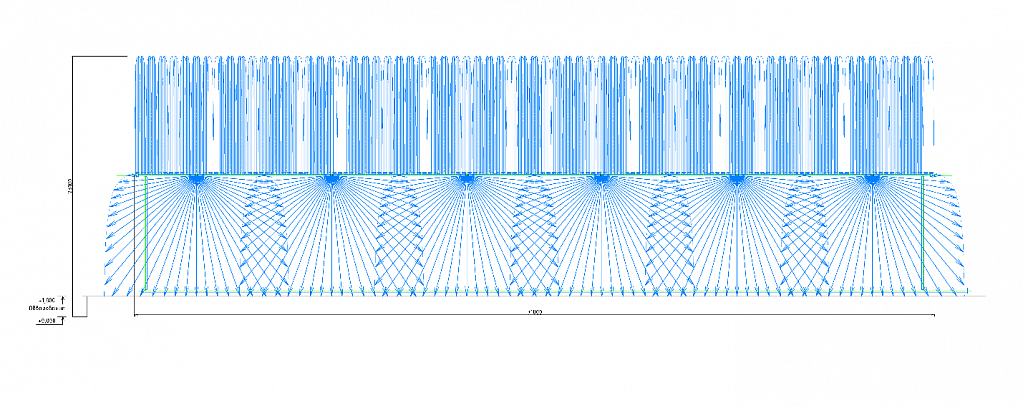
An example of a water curtain for industrial facility with Pozhneftehim deluge sprinklers. The length of the water curtain is more than 71 meters, the height is more than 23 meters.
To restrict spreading LPG vapor when it spills and leaks along the dike perimeter, it is recommended to provide steam or water curtains. Localization of LHG vapor is achieved by dragging it up by water sprayed jets or water vapor and diluting them with air to concentrations below the LFL. These curtains should be launched immediately after the accident. For this end, the water (steam) supply system must be switched on automatically from the signaling devices activated by pre-explosive gas concentrations. Please read more about high-altitude water curtains with the Pozhneftehim equipment here.
Foam fire extinguishing installations within the diked LHG isothermal tank site
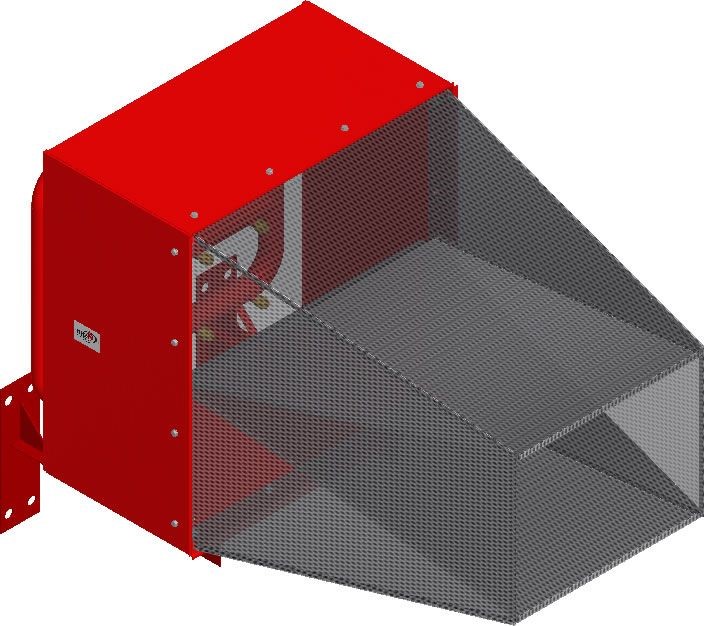
Favorit high expansion foam generator, manufacturer: the Pozhneftehim Group
For fire protection of the LHG diked tanks (quick fire localization and flame reduction due to the insulating foam layer), recommended is the application of an fixed automatic foam extinguishing system operated by high-expansion foam generators of increased productivity. Such a foam generator creates a foam of 700-800 expansion without air charged by electric fan. Pozhneftehim recommends using the Favorit high-expansion foam generator within the diked LHG tanks site Favorit high-expansion foam generator
The fixed high-expansion foam extinguishing installation includes:
- an LHG fire/spill detecting and warning system and sensors within a dike;
- water supply system switching device;
- foam concentrate device to portion it into a dry pipe line;
- containers with a synthetic foam concentrate suitable for producing high-expansion foam;
- high-expansion foam generators mounted on the dike edge.
To protect the open processing equipment within the diking (shutoff valves, pipelines, hatches into tanks), foam generators should be located along the diking edge so that the diked area is filled with high-expansion foam with a layer height covering all processing equipment, but not less than 2 m, for 10 minutes.
One automatic fixed installation can serve several protected objects, including open processing installations. The maximum time from the moment a fire is detected until the foam reaches the diked site should not generally exceed 3 minutes.
IF YOU HAVE QUESTIONS OR PROPOSALS, PLEASE FILL IN OUR FORM
Filling out the form means you agree with the confidencial policy of the web-site www.pnx-spb.ru and agree to receive the email by Pozhneftehim-Expert to the indicated email. You can unsubscribe from the email at any time. You can also get access to emails that were send before. The contact email for the Pozhneftehim-Expert project is expert@pozhneftehim.ru.
PRODUCTION DIRECTIONS OF POZHNEFTEHIM-DETAL
Pozhneftehim produces a wide range of equipment for fire extinguishing systems and installations. These are foam generators of low, medium, high expansion, fire filters, fire monitors, fire towers, stabilizers, interlayer nozzles, fire equipment connection nodes, etc.
Foam concentrate dosing systems with turbine inline, balanced pressure and foam inductor proportioners. Production of containers (tanks) for storage of foam concentrate and piping arrangement.
Pozhneftehim has been producing custom-made bladder tanks since 2010. We supply products with a full set of permits and operational documentation including factory test reports.
Custom-made block-modular structures: block containers, fire hydrant units, foam cabinets. Block-modular products of Pozhneftehim are equipped with equipment, systems and installations in accordance with the requirements of design documentation.