BLADDER TANKS “ANTIFIRE”
Pozhneftehim has been manufacturing the bladder tanks “Antifire” at its own production site in Tula Region (Donskoy) since 2010. All the products meet the requirements of ISO Standards. There is a hydraulic testing site for quality control of bladder tanks and equipment for firefighting systems at the plant.
Bladder tanks “Antifire” are custom-made in accordance with configuration data sheets and technical specifications of firefighting system. Pozhneftehim specialists provide consultation on the issues related to the design documentation of firefighting systems, perform supervised installation and commissioning of bladder tanks at the Customer’s facility, as well as aftersales service (including filling and refilling) of the tank.
Fast Facts:
Available Versions of Bladder tanks Manufactured by Pozhneftehim
Antifire Horizontal Bladder tank |
Antifire Vertical Bladder tank |
Antifire Double Bladder tank |
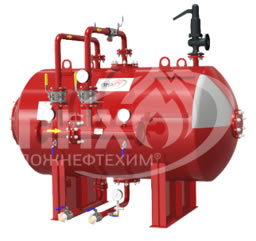
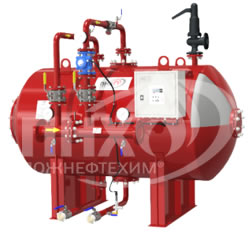
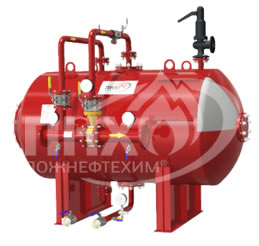
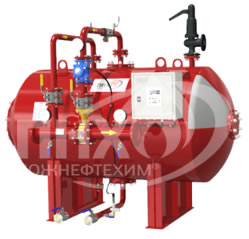
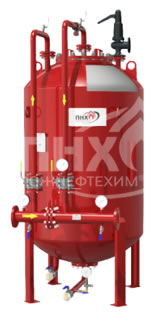
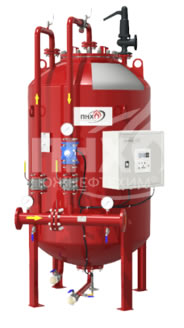
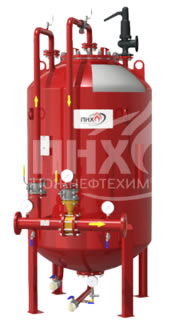
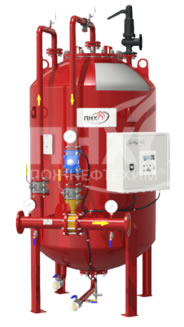
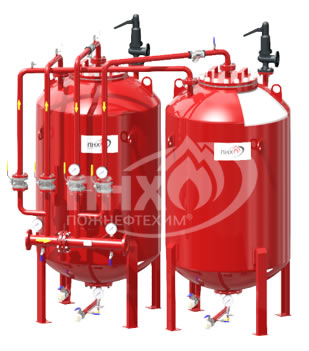
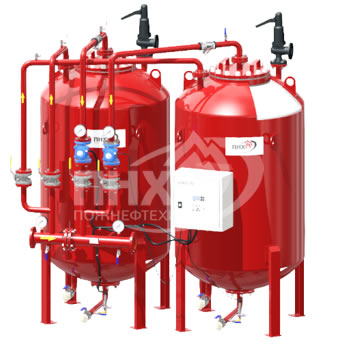
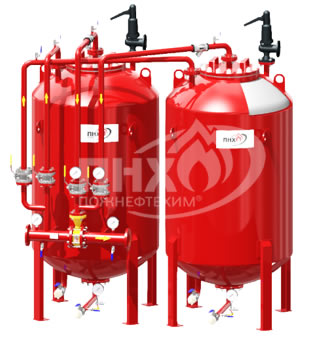
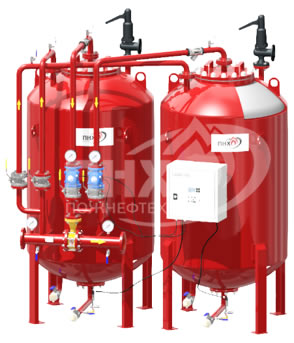
When purchasing a bladder tank, please, check if the specified parameters and configuration meet the requirements of the design documentation.
Notes for Purchase Department on Choosing and Purchasing Bladder tank (pdf, 7 Mb).
Bladder tank “Antifire”. Technical characteristics
- Dosing – 0.5, 1, 3, 6 % (on request)
- Range of water flow according to nominal inlet pressure and DN of dosing unit (on request)
- Service life – not less than 25 years
- Nominal inlet pressure of bladder tank – 0.4-1.2 MPa (at option on request)
- Loss by dosing unit – not more than 0.02-0.25 MPa
- Range of operational pressure – 0.4-1.4 MPa
Bladder tank Design Features
Computer-Controlled Monitoring of Foam concentrate level (para. 5.1.7, para. 5.1.12 GOST R 50800) |
Supplied with Control Cabinet (ShABD) of Bladder tank and set of control instruments |
Foam concentrate Mixing (para. 5.9.26 SP 5.13130) |
Foam concentrate mixing function (on request) |
Quality Parameters
Availability of testing site for Functional Testing of Bladder tank |
|
Inner Flexible Container Characteristics |
Material: hypalon-neoprene, strength: not less than 300 daN/5 cm Strength of inner flexible container neck – pull test at the load of not less than 3500 N |
Inner Corrosion-Resistant Coating |
Finish two-component epoxy enamel, coating thickness: 300 (±30) µm. Technical Justification of Specifications, Technology and Certificate of Conformity are supplied on request |
Outer Coating |
2 layers of epoxy primer, each of 50-60 µm, 1 layer of polyurethane enamel 60-80 µm (standard) Three-layer coating (enamel, primer). Thickness of finish coating: 180-220 (±22) µm (on request) |
Technical Specifications and version of Component Parts correspond to the characteristics of foam concentrate and the foam solution (premix) |
|
Dosing Membranes |
12Kh18N10T Stainless Steel |
Ball Valves on Water Supply Line to Tank and on Foam Compound Supply Line from Tank to Dosing Unit |
|
Return Valve on Foam Compound Supply Line |
Material: stainless steel |
Filter on Water Supply Line to Tank |
Material: stainless steel |
Pressure Gauges on Dosing Unit and on Foam Compound Supply Line from Tank to Dosing Unit |
Glycerin-filled, casing material: corrosion resistant steel, pipe union material: copper alloy |
Pressure Sensor on Foam Compound Filling Line | Glycerin-filled, casing material: corrosion resistant steel, pipe union material: copper alloy |
Basic Configuration of Bladder tank includes:
Control Cabinet (ShABD) displays volume of foam concentrate in the flexible container. The device displays and archives data on foam concentrate level, thus complying with the requirements of para. 5.1.12 of GOST R 50800.
Flexible Container (standby) can be supplied together with bladder tank to provide for prompt replacement of working container in case of its failure (during filling or refilling by workers other than manufacturer’s specialists).
- Tank with inner flexible container, dosing unit with fitting, ball valves on water supply line to tank and on foam compound supply line to dosing unit
- Safety valve on water supply line to tank with nominal pressure of 1.6 MPa
- Return valve on foam compound supply line from tank to dosing unit
- Branch pipes for tank filling with foam compound
- Flowmeter
- Pressure gauges on dosing unit and foam compound supply line from tank to dosing unit
Optional Configuration of bladder tank includes:
Dosing Membranes |
12Kh18N10T Stainless Steel |
Ball Valves on Water Supply Line to Tank and on Foam Compound Supply Line from Tank to Dosing Unit |
Full port, ball material: stainless steel (when ordering fitting from standard steel) Full port, material: stainless steel (when ordering fitting from stainless steel) |
Return Valve on Foam Compound Supply Line |
Type: couple, interflanged Material: stainless steel |
Filter on Water Supply Line to Tank |
Type: interflanged Material: 09G2S Steel, stainless steel |
Pressure Gauges on Dosing Unit and on Foam Compound Supply Line from Tank to Dosing Unit |
Glycerin-filled, casing material: corrosion resistant steel, pipe union material: copper alloy |
Flowmeter (Pressure Gauge) on Foam Compound Filling Line |
Glycerin-filled pressure gauge. Casing material: corrosion resistant steel, pipe union material: copper alloy |
Cut-off Valve for protection of Flowmeter (Pressure Gauge) against increased pressure |
Stainless steel |
Please, consider the quality-to-price ratio when choosing and purchasing bladder tank.
Pozhneftehim offers bladder tanks “Antifire” from high quality materials. Our bladder tanks undergo testing at the testing site and correspond to the design documentation of сustomers. The characteristics of bladder tanks meet the requirements of the Customer’s design documentation. When necessary, our Service Department specialists can provide for filling/refilling during commissioning, training of personnel on operating instructions for bladder tanks. When ordering the bladder tank together with the Pozhneftehim foam concentrate “Aquafom”, additional warranties are provided for foam concentrate storage in bladder tank.
If you want to see operation of the bladder tank as part of firefighting systems and installations, you can sign up to the Advanced Training Courses offered by Pozhneftehim. These are annual training sessions which include testing of firefighting systems and discussion of topical matters related to the design of firefighting systems, development of Special Technical Conditions, selection of firefighting techniques and equipment, selection of foam concentrate taking into account facility features, etc.
IF YOU HAVE QUESTIONS Or PROPOSALS, PLEASE FILL IN OUR FORM
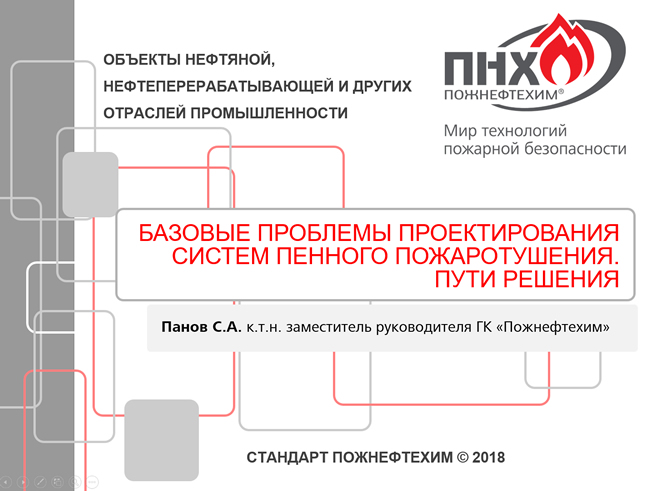
Стандарт Пожнефтехим "Базовые проблемы проектирования систем пенного пожаротушения. Пути решения". 2018 (pdf, 2.32 Mb)
Contact information to order Pozhneftehim complex supplies:
Questions concerning the choice of foam concentrates for fire extinguishing
Tatyana Potapenko, foam project manager +7 (499) 703 01 32, ext.172
Questions concerning the choice of firefighting equipment
Sergey Vypritsky, Project Manager +7 (499) 703 01 32, ext.153
Questions on documentation regarding Fire safety measures (MOPB) and Special technical conditions (STU)
Sergey Titenkov, Head of Regulatory and Technical Department +7 (499) 703 01 32, ext.159
